モーターコア製造業の現場を一部お見せします!
製造業で働いた事はありますか?学生時代(もしくは現在学生の方も)、コンビニやスーパー、サービス業でのアルバイト経験がある方は多くても、製造現場(特に弊社の様な業種)で仕事をした経験がある方は少ないのではないでしょうか。この記事では老舗製造業の松本ESテック株式会社従業員が、どの様な流れで製品を作り出しているかを、工程ごとにご紹介いたします。誇りとこだわりを持って働く弊社社員たちの一日を是非ご覧下さい!
松本ESテック株式会社の製造現場
「電磁鋼板スリット加工販売」「モーターコアを製造販売」する弊社は製造業の会社です。工場ごとに工程やグループに分かれており、仕事内容や始業時刻、働く社員の個性もそれぞれです。普段はご覧頂く機会がないリアル製造現場をのぞいてみましょう!
本社、幕張工場
幕張工場では電磁鋼板をロール状に巻いた素材を必要な幅にカットし(この工程をスリットといいます)梱包してお客様先に出荷したり、次工程がある白井工場へ材料として供給したりしています。入荷する素材の電磁鋼板は板の厚みが一定でなかったり、時にはさびやキズがあったりする事もあるので細かいチェックが必要です。工場内には天井クレーンがあるため天井がおよそ10メートルと高く、場内の空気調整が難しい事もあるため、スポットクーラーやストーブなどで対応しています。
スリット工程の1日
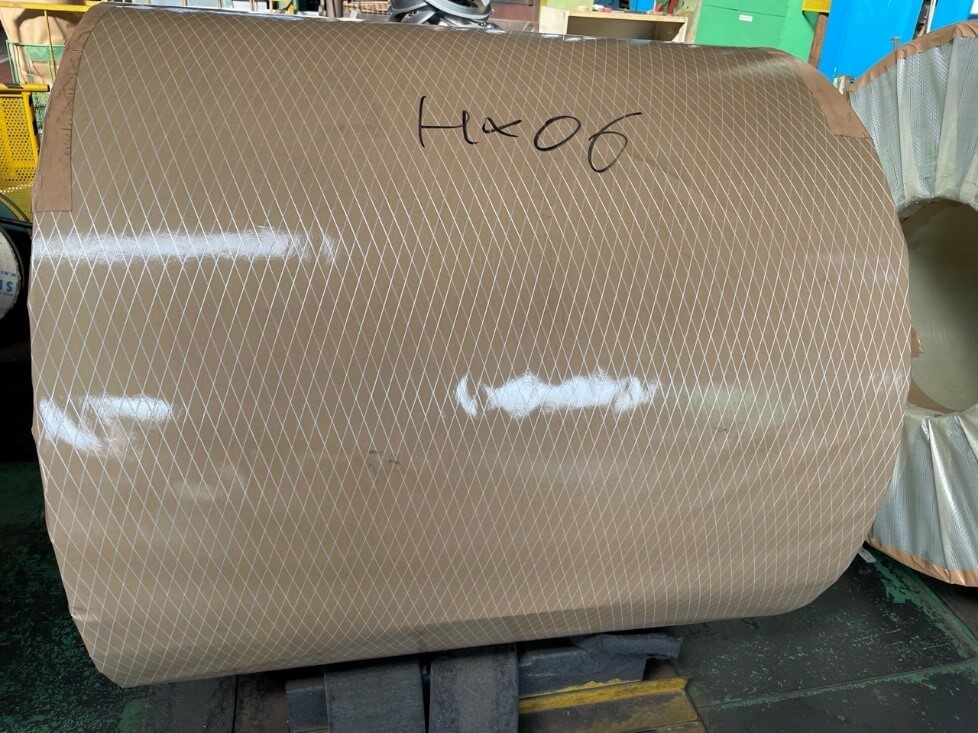
始業:8時(7時30分の社員もいます)
- 朝のミーティングで生産計画確認
- 使用する電磁鋼板の梱包紙を剥がし、外観にさびやキズが無いかチェックします。
- スリット加工する電磁鋼板をアンコイラーという設備にセットします。材料の幅はおよそ1,000㎜、質量5〜9tです。アンコイラーへのセッティングは有資格者がクレーンを操作して行います。
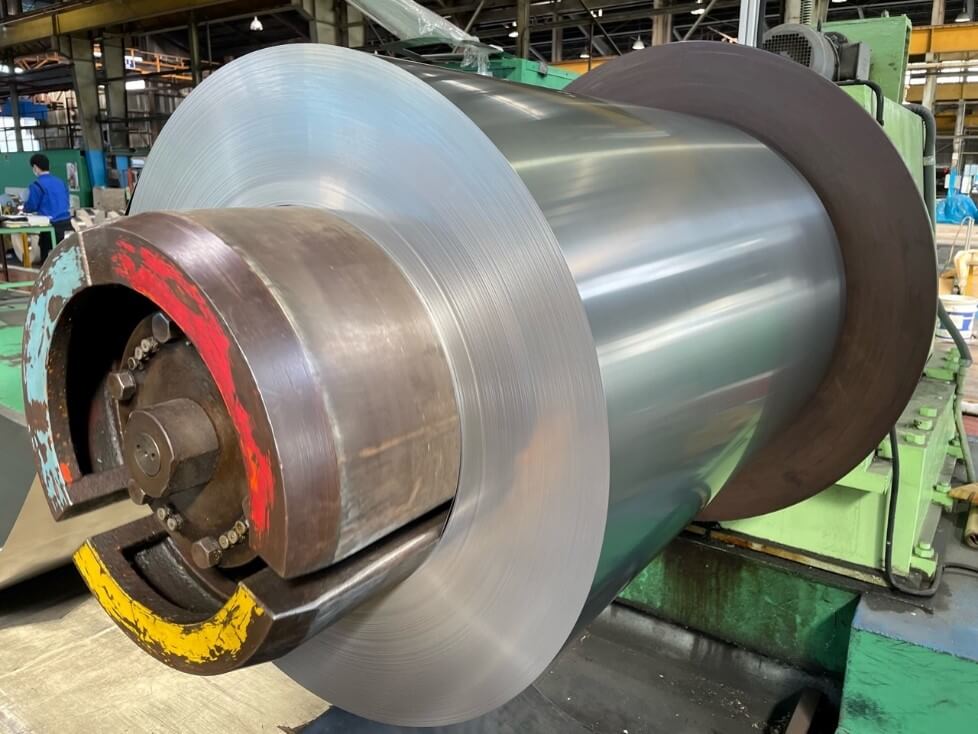
4. お客様のお客様の注文に合わせてカッターの刃とスペーサー(幅を一定に固定させるための道具)を組合せ(刃組…ハグミと言います)、スリットする 幅を設定します。上下の回転刃には隙間(ギャップ)があり、このギャップが適性でないとカットした材料の端が滑らかではなくなり、製品として出荷する事ができなくなってしまうこともあります。
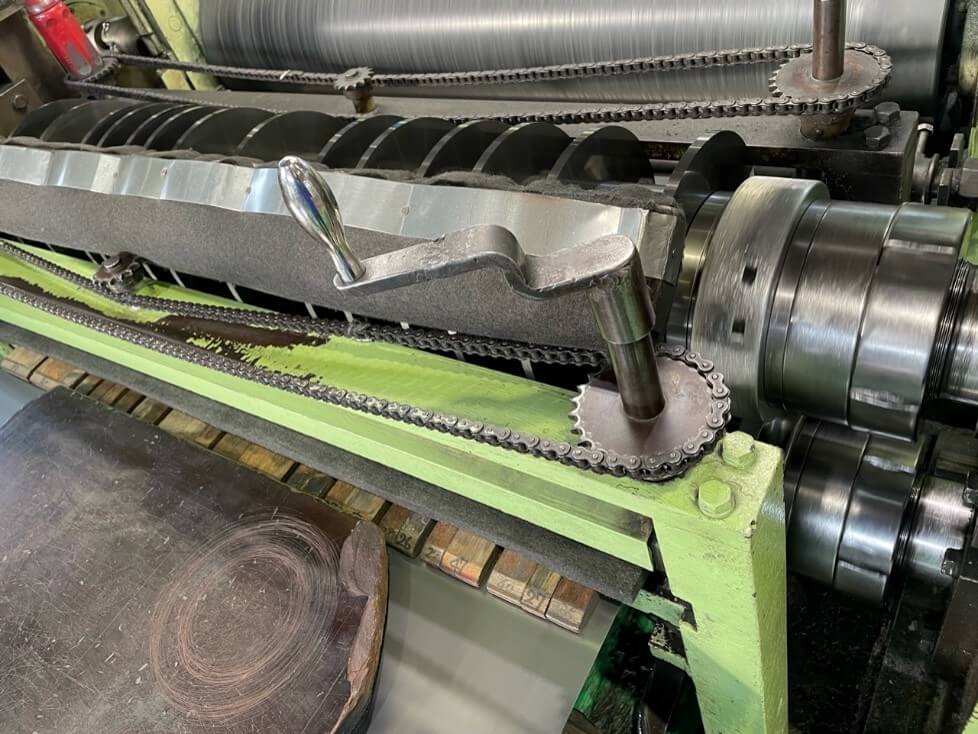
5. カットされた電磁鋼板はリコイラーと呼ばれる巻き機によってふたたびロール状に巻き直します。電磁鋼板の厚みや幅などによって「強すぎず、弱すぎない」適正な張力にコントロールする必要があります。この作業中に電磁鋼板に穴やキズなどがないか目視検査を行い、再加工に回される電磁鋼板もあります。
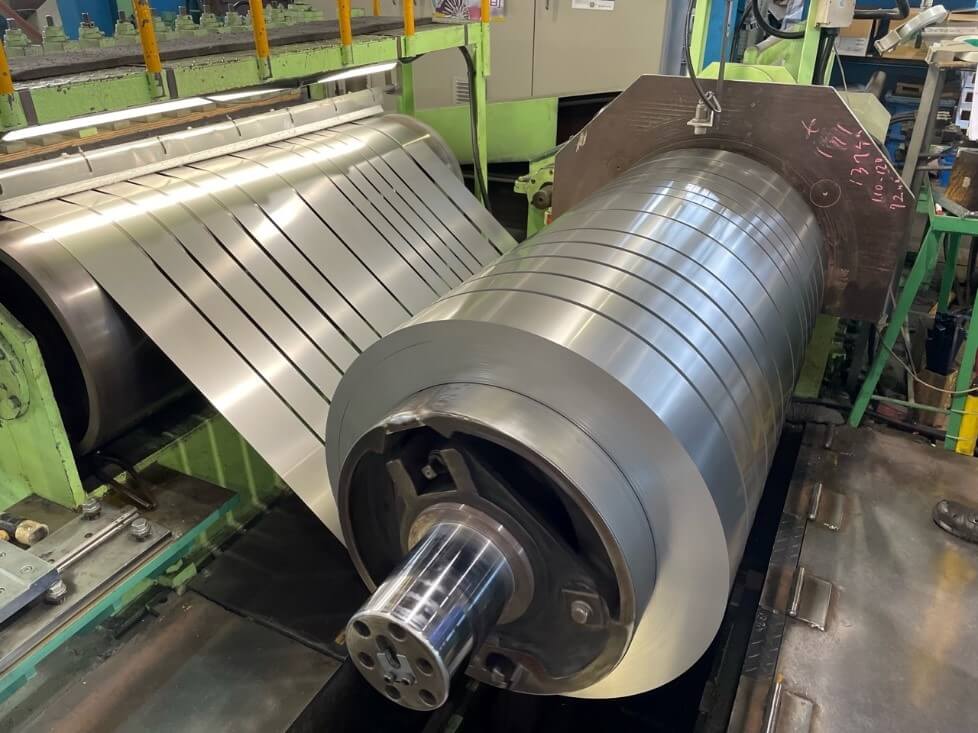
6. スリット加工が完了です。適正な張力で巻かれているため芯が無くても崩れにくいです。
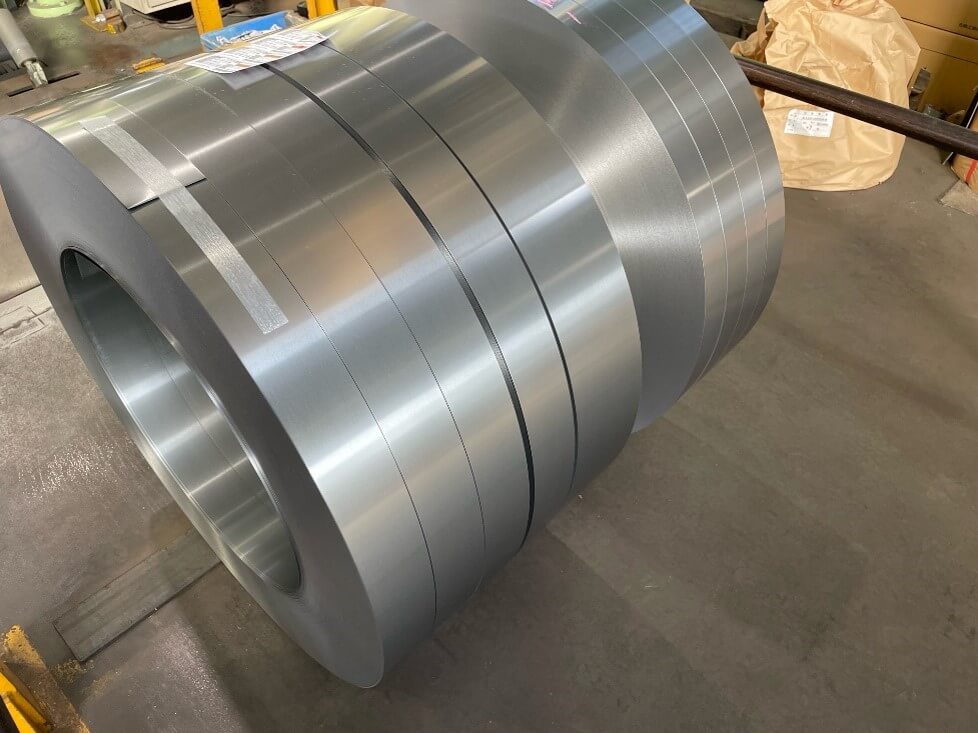
7. スリット完了後の製品は移動や保管時にさび、キズ、折れなどが発生しないように取り扱いには細心の注意を払う他、電磁鋼板は重量物の為、周囲の人の動向にも常に注意しながら作業しています。
8. お客様の指示に従い専用の梱包機できれいに梱包し出荷を待ちます。
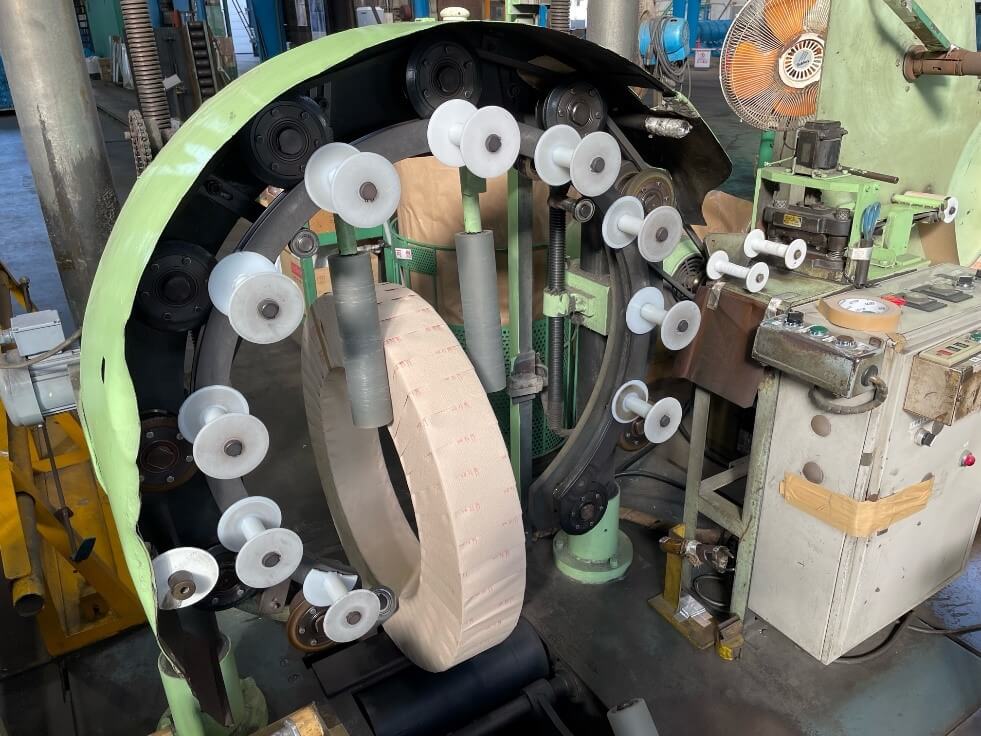
9. 天井クレーンで移動し、トラックに乗せて出荷します。
途中、お昼休憩45分、15時~休憩15分を挟みながら上記4~9までの作業を4回程度繰り返します。
白井工場・白井第二工場
幕張工場でスリットした電磁鋼板を加工する工場です。成形後お客様の注文に合わせて更に加工を施す工程もあります。弊社事業所の中では設備、敷地ともに最も大きく、弊社の主力製品である「モーターコア」を製造しています。
プレス加工の一日
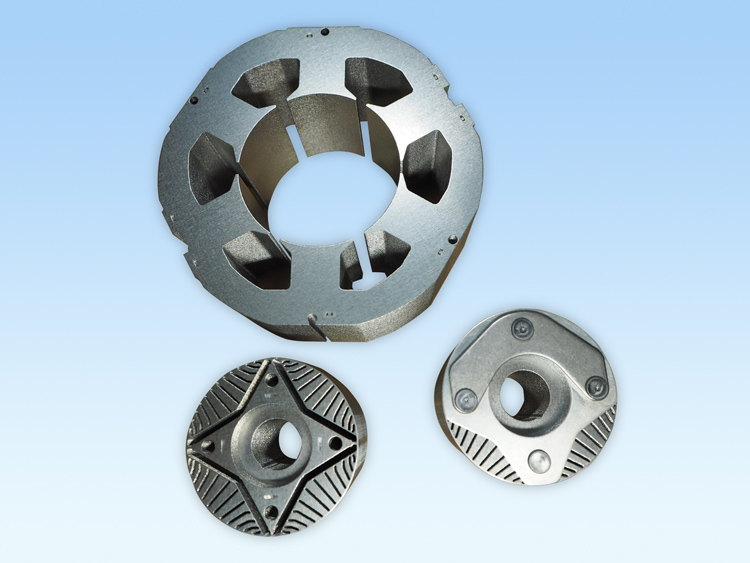
幕張工場でスリットした電磁鋼板を打ち抜いて成形する工程です。この工程で使用している高速精密プレス機の中には国内有数の最新型設備もあります。お客様が必要とするモーターコアの形状、特性はそれぞれ異なるため、製品を打ち抜くためにプレス機内にセットする型(金型といいます)を替える重要な作業もあります。
始業:8時30分(夜勤者は20時30分~)
- ミーティングで生産計画確認(変更、遅れのチェック、伝達事項等の周知)
- 幕張工場から運ばれた電磁鋼板をクレーンで移動し、機械にセットするなどの段取りを行います。
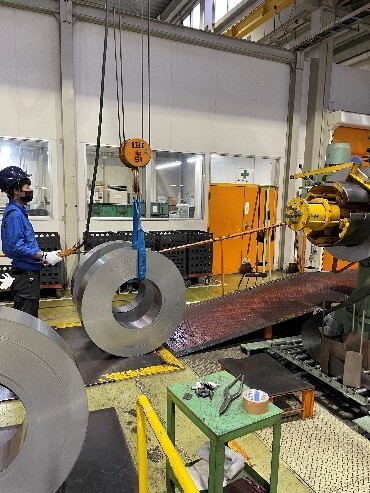
3. 高速高速精密プレス機は毎分260~300ショットのスピードで電磁鋼板を打ち抜き、積層後に圧をかけて製品を作り上げます。全て自動運転で行われています。
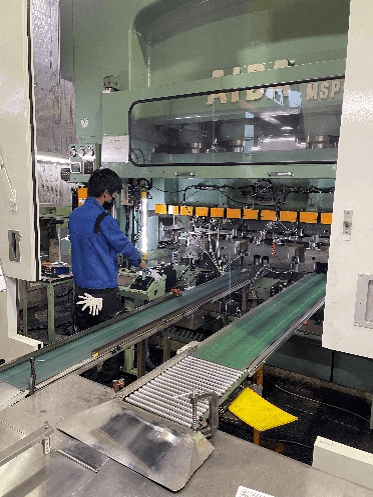
4. プレス加工された製品を特定の計測器・検査治具(ノギス、ゲージ、測り等)を使用してお客様が必要とする規格に適合しているか、製品精度の検品を行います。
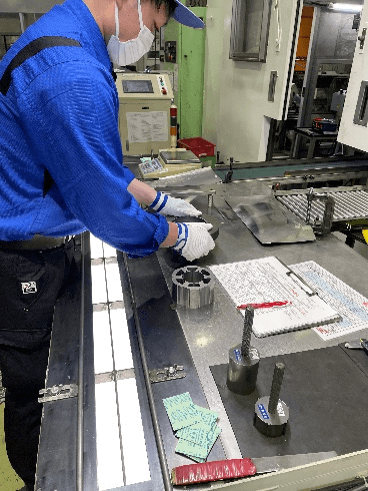
5. 規格適合と判断された製品を指定の梱包箱に詰め、輸送梱包形態に仕上げていきます。
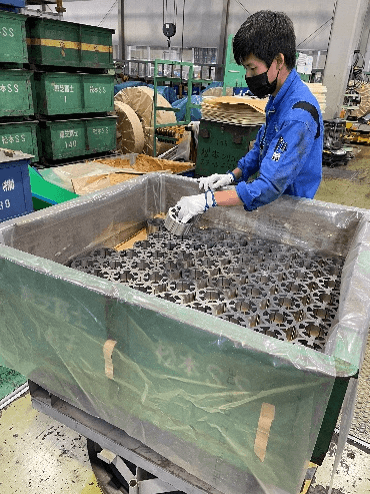
6. 輸送梱包形態に仕上がった製品入りの梱包箱を、電動フォークリフトを使用し保管場所に移動します。
上記、1~6が量産プレス加工の作業の流れです。
その他、付帯作業として
- 生産する製品の種類が変更になった場合は、製品を打ち抜くためにプレス機内にセットする型(金型)を乗せ換える作業を行います。(この作業はとても重要、且つ時間を要する作業でベテランでも型替えを終了し稼働するまでに8時間かかる場合もあります)
- プレス機に付属する周辺設備の部品変更作業(制御盤、補助設備、その他設備の設置、設定など)
ローター組立工程
この工程ではお客様のご要望に合わせて小型のモーターコアにマグネットや指定部材などの部品を取り付ける作業を行っています。エンド工程のため上工程からの影響を受けやすく、不適合品の流出防止のチェックと納期厳守意識の高い工程です。
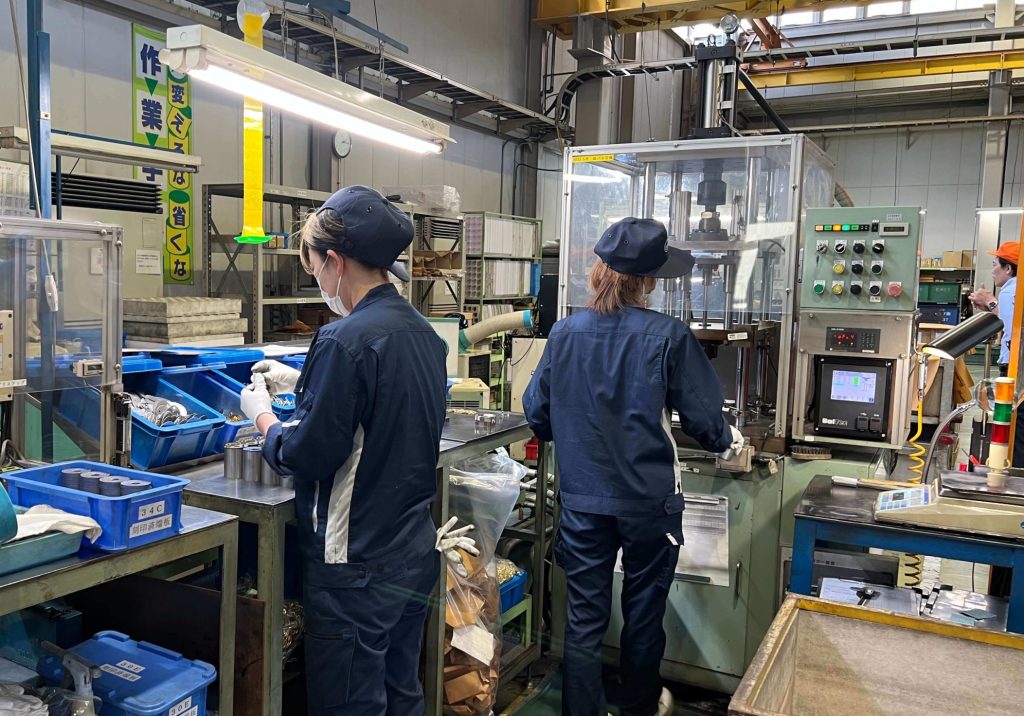
始業:8時30分
- 製造指示確認
- ローター(回転子)コアと取り付ける部材を準備します。(生産機種が多い為段取りを少なくするための事前計画、準備も重要です)
- 作業台に移動します。
- モーターコアのマグネットを挿入します。
5. マグネット挿入後、落ちない様に蓋の様な部材を取り付けます。
6. 仮のカシメ機にセットし、仮カシメをします。(カシメとは、溶接、接着剤、ネジ・ボルトなどを使用せずに板金を締結できる加工方法です。)
7. 仮カシメした製品を本カシメ機にセットし、本カシメします。
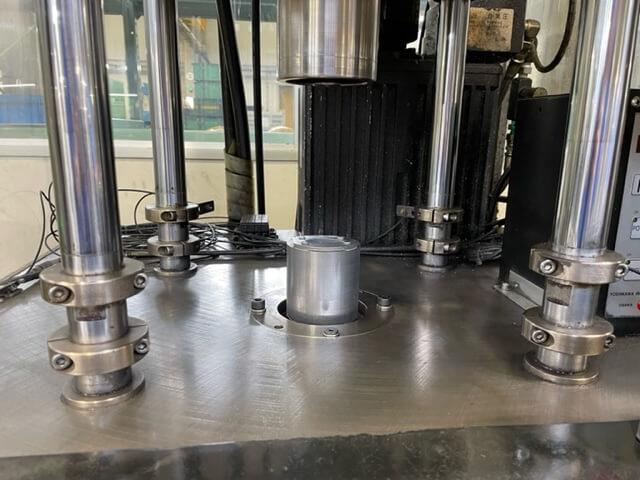
8. 本カシメ終了後検査表(規格が記載されています)の項目に従い製品をチェックします。ここで不適合品を確実に見分ける事が不良品流出防止につながる、とても重要なチェックです。
9. 適合品はステンレスの箱に入れ、次の焼鈍工程へ運びます。
10. 焼鈍工程で加工油等の付着物を除去し再び、組立工程へ移動し、出荷梱包工程で製品確認を行い客先へ納入します。
焼鈍工程
プレス工程、ローター組立工程から引き継いだモーターコアを焼きなます工程です。製品を焼く炉の温度は780度にまで上がり、炉の温度を下げない管理が必要となるため、稼働期間中は24時間体制の工程です。モーターコアが入った鉄箱を焼鈍炉に入れ、約9時間焼きなまし、取り出して冷まし製品が完成します。
始業:8時30分(夜勤者は20時30分~)
- プレス工程で加工した製品をクレーンで移動し、連続自動焼鈍炉の処理トレイにセットします。
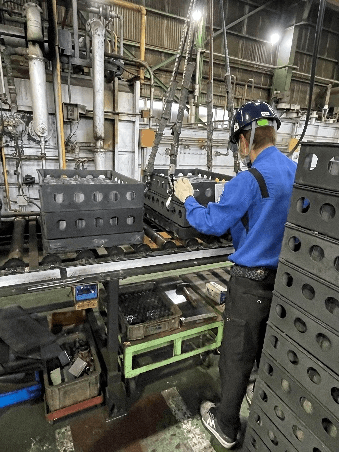
2. 焼鈍炉で9時間程度焼き鈍した製品を取り出し、クレーンで移動専用のパレットに適量セットし、電動フォークリフトで移動します。
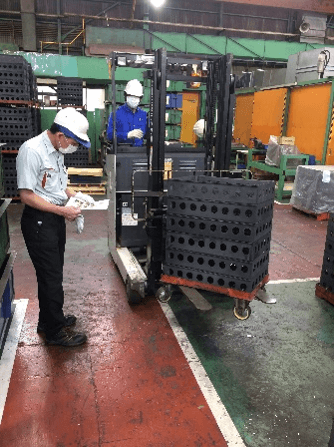
3. 移動した製品を目視検査で検品を行い、合格と判断した製品を指定された梱包箱に詰め、輸送梱包形態に仕上げます。
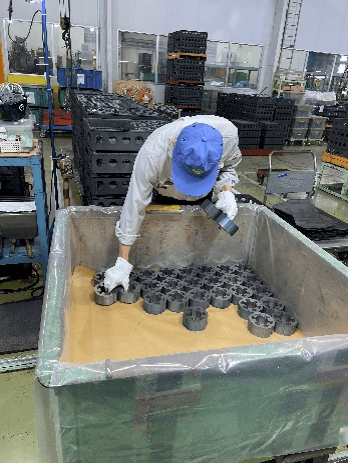
4. 仕上がった製品入り梱包箱を電動フォークリフトを使用し保管場所に移動します。
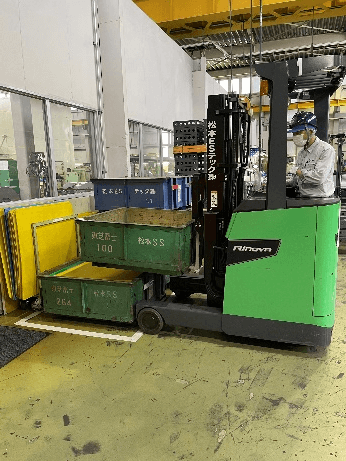
上記、1~2が焼鈍処理加工の設備オペレート作業、3~4が焼鈍工程の箱詰め作業です。
5. 焼鈍工程では焼鈍炉のトラブルが発生すると大量の不良発生につながる為、常に「設備保全」「梱包」「処理部材」には特に注意を払いながら従事しています。
その他、付帯作業として
- 焼鈍炉保全作業で各確認事項を決められた時刻に確認し記録を残します。
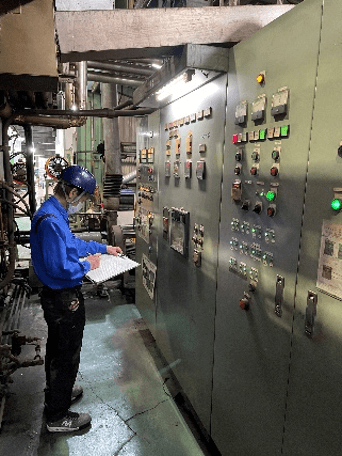
製造技術工程(金型メンテナンス)
プレス加工機で使用する、製品を造り出す要である「量産順送金型」をメンテナンスし、維持、管理している工程です。メンテナンスでは金型を分解、研磨したり、丁寧に掃除をしたりしながら組み上げて元の金型に戻していきます。金型の精度を維持し管理する技術と、プレス生産時のトラブルにもスピーディーに対応できる体制が弊社の強みでもあります。
始業:8時30分
- プレス工程で使用する金型は生産ショット数で管理され、定期メンテナンスショット数を迎えた金型は定期メンテナンスを実施します。
- 金型を分解し、平面研削が可能な状態に組み上げます。
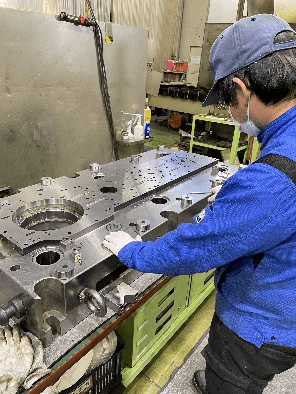
3. 組み上げた金型の刃先を平面研削盤でシャープエッジに研削し、切れ味を再生させます。(ミクロン単位で削ります)
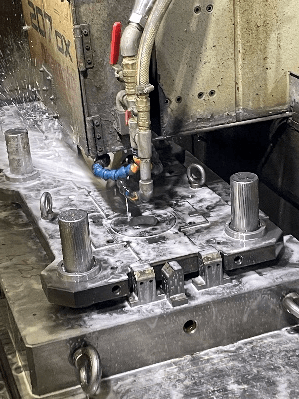
4. 研削加工が終了した金型は洗浄工程で汚れ・異物などをきれいに取り除きます。
5. 洗浄工程が終了した金型を再びプレス工程で使用できる設定に組み上げていきます。
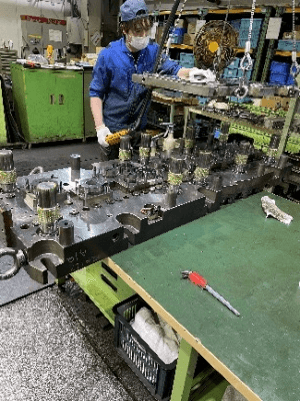
6. 組み込み作業が終了した金型は、設定状態に間違いがないか特定の計測器(ダイヤルゲージ、ハイトゲージなどの複数のゲージ、ノギス、マイクロメータなど)を使用して検査を行います。
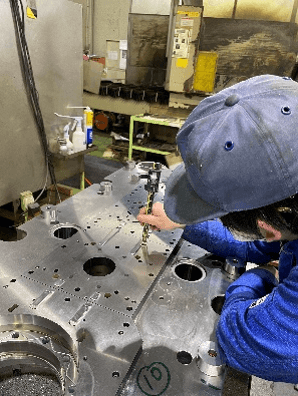
上記、1~6がプレス金型のメンテナンス作業工程です。金型メンテナンス業務を行うには、クレーンの操作が必須となります。
その他、付帯作業として
- プレス工程での金型トラブル時にはスピーディーに対応できる様、常に体制を整えます。
- プレス工程で使用する金型の準備作業、クレーンを操作し、保管場所への移動も行います。
- 金型管理帳票の記録入力、確認整理をする事で金型の状況を把握します。
製品の仕上がりを左右するこの一連の作業は、熟練者でも1つの金型メンテナンス完了までに2~3日かかります。この作業で独り立ちするには定期メンテナンスのみでも約2年を要します。
製造技術工程(試作)
量産を見据えた試作案件に対応しているグループです。試作品の金型や治具(材料を固定し、加工が正しく行われるための補助的な役割をもった装置)の設計、製作にも対応できる技術を持ち合わせています。試作のため製作する金型の精度調整や、電磁鋼板を打ち抜き・カシメ突起の出代調整など、お客様先の規格要求を満たすためには、ミクロン単位での調整が必要になります。
- 営業部より試作依頼が入ります。
- 2次元CADで試作品の図面を起こし、必要な金型と積層治具製作のための図面を起こします。
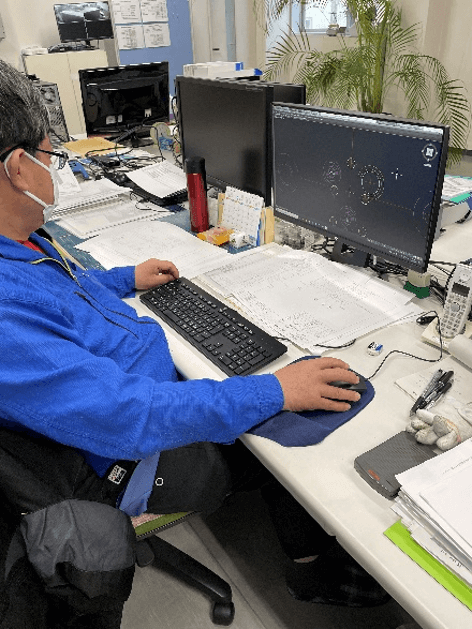
3. 図面に従いワンパンチ試作用の金型と積層治具を製作します。
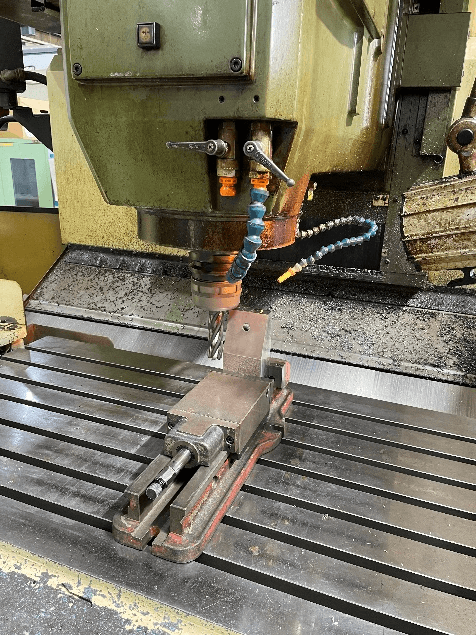
4. 出来上がった金型をワンパンチプレス機(手動で一枚一枚電磁鋼板を打ち抜く機械です)で打ち抜きます。
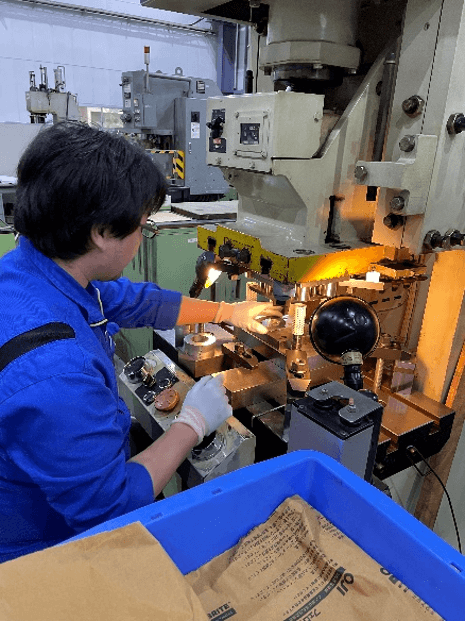
5. 積層治具により、打ち抜かれた電磁鋼板を正しい位置でおよそ70枚~300枚程度積層させ(製品や使用する電磁鋼板の厚みによって異なります)、最後に接合させるための突起(カシメ突起と言います)を変形させて試作品が型になります。
6. 工程内検査ではノギス・マイクロメータを使用して積厚検査及び外観検査を行います。お客様先によってはダイヤルゲージ・三次元測定器による端面振れ測定他各部位の精度検査をご依頼を頂く事もあります。
7. 品質管理部門で最終検査を行い試作品が完成します。
鶴岡工場
唯一看板方式を取り入れている工場です。少数精鋭工場という事もあり、必要に応じて必要な生産を行うため1日の流れは日によって異なります。
(鶴岡工場の始業は全工程8時からです)
プレス工程
(作業手順は白井工場プレス工程とほぼ同じです。)
ダイカスト工程
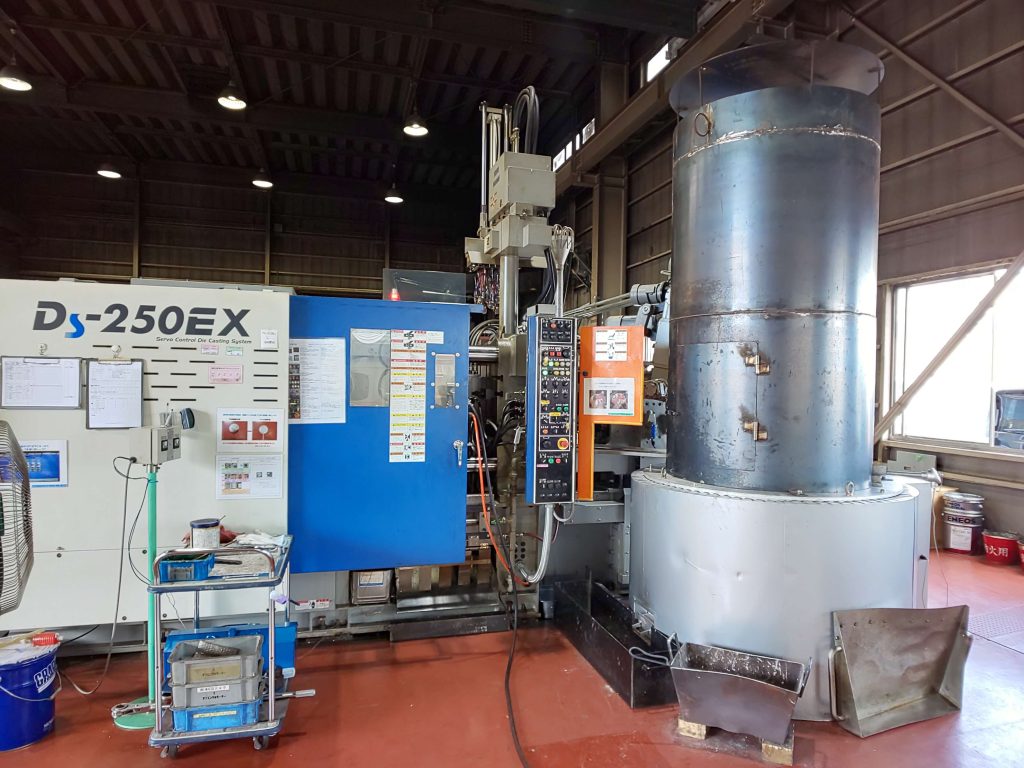
ダイカスト工程はローター(回転子)にアルミ純度99.7%以上の塊を電気溶解炉で溶解し付着させる工程です。
- ローターをダイカストマシンの投入レーンにセットします。

2. ローターが5個同時に自動でダイカストマシンの金型内に搬入され、溶解したアルミが金型内に射出されます。(溶解したアルミの温度は730度です)
3. 約1秒後に金型が開き、ローターにアルミが成形付着された製品を取出し装置が受取り、同時に次のローターが金型内にセットされます。
4. 金型内から自動で運ばれたダイカストローターは担当者が目視検査を行い、梱包します。

5. 50秒/1サイクルで1日に2,000台以上生産しています。
ルミラー挿入工程
この工程は弊社では鶴岡工場のみが行っています。ルミラー挿入とは絶縁フィルムをステーター(固定子)に挿入する工程です。
- ステーターのスロット(24スロット/1台)というコイル線が入る箇所全てに絶縁フィルムが入ります。

2. 完成したステーターは内径検査治具とスプライン(フィルムの飛び出し検査用の治具)で検査します。
3. 最後に目視検査でさびやキズ、フィルム状態を確認し梱包します。生産時間は1台当たり約12秒です。

リップローター工程
ダイカストされたローター(回転子)にモーター軸を圧入する工程です。
- ダイカストローターにモーター軸を圧入します。
- 専用治具で挿入精度検査実施します。(値3μ~30μの振れ幅)
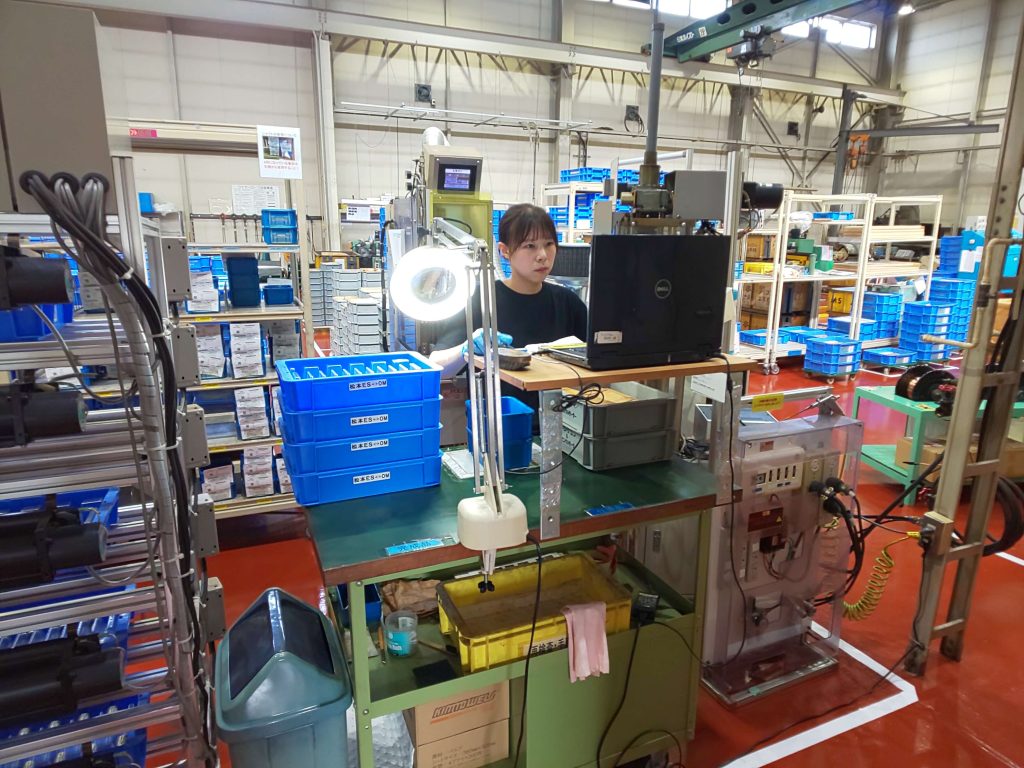
3. 製品を専用の洗浄機で、防錆油の噴射で洗浄します。(洗浄済みの打痕が付きます)
4. 打痕の確認と目視検査を行い製品を乾燥させて箱詰を行います。
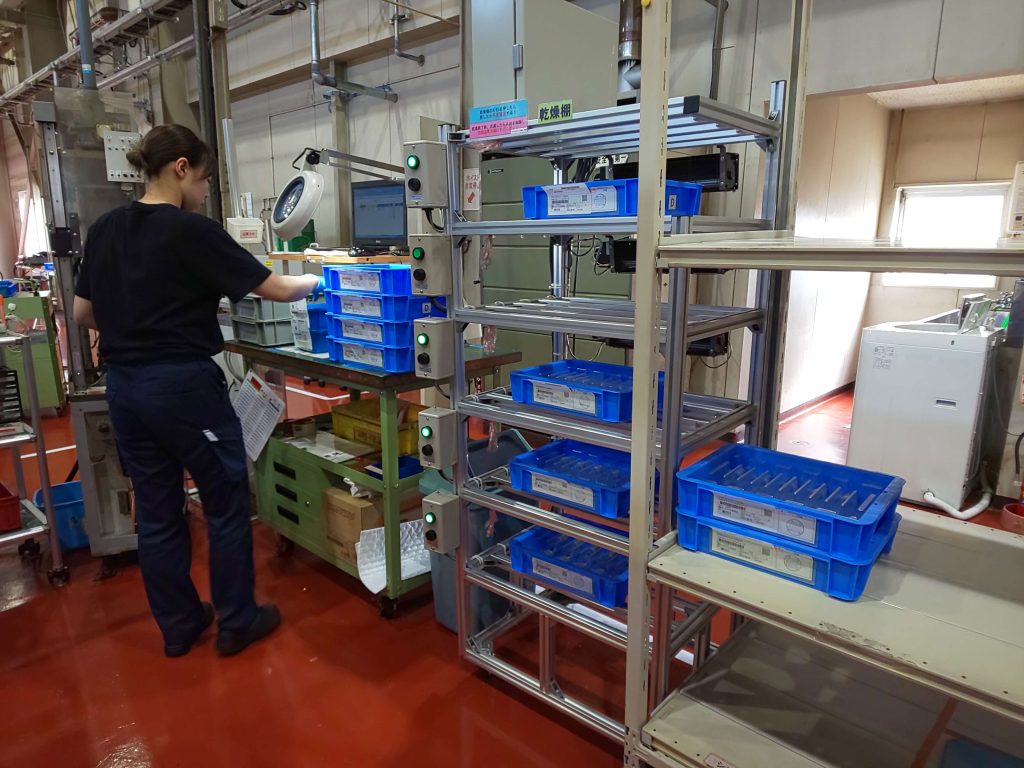
まとめ
見慣れない製造現場の様子から、働いている弊社従業員を想像していただく事ができたでしょうか?どの工程にも存在している「ミクロン単位の細かい作業」やマイスター的な「こだわり」には必ず意味があり、それは「最高の製品をお客様に提供する」という松本ESテックの「使命」から生まれるものです。私たちはこれからも継承し続けている技術を大切にしつつ、進化する社会に対応できる様、最新の技術も学べる現場を目指します。