電磁鋼板加工の老舗「松本ESテック株式会社」をご紹介
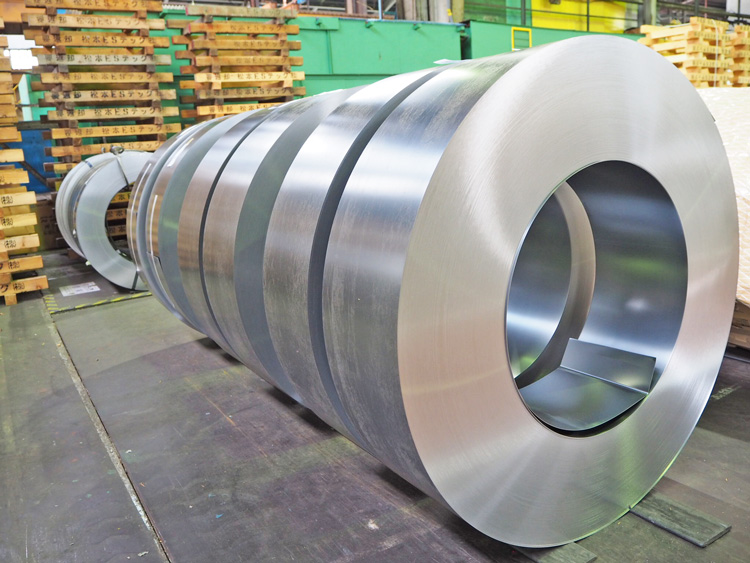
ホームページや求人広告、会社パンフレットに記載されている会社の情報。もっと詳しく知りたい!本当はどうなの?と思ったことはありませんか?そんな方必見!今回は電磁鋼板加工の老舗「松本ESテック」を知っていただくために、できる限り分かりやすく、弊社の歴史から各工場ができるまで、そして工場の特長や各工程の作業内容、当社の優位性などをご紹介します!
電磁鋼板を加工する業界では有名です
松本ESテック株式会社は創業以来76年間、日本トップクラスの技術で電磁鋼板を加工しモーター産業を支え続けている、モーターの心臓部分「モーター・コア」を製造している会社です。先ずは46年間の歴史をひも解き、各工場ができるまでのその道のりを辿ってみましょう。
創業者と電磁鋼板との出会い
戦時中は陸軍の地上短波探知機の研究員、復員後は通信機器メーカーの技術者として研究所に勤務していた弊社創業者である「松本兼吉」は、同社での技術開発に携る中で、発展途上の素材である「電磁鋼板/ケイ素鋼板」に興味を持ちます。時代の流れから職を離れることになった兼吉は、ここで運命的な出会いがあります。知人からの紹介で、研究員時代に興味を持っていた「電磁鋼板」の販売を持ち掛けられたのです。研究者から営業への道に不安を抱きながらも「松本商店」を立上げ、販売代理店としての商売が始まります。
販売代理店から加工販売へ
前職での人脈や兼吉のバイタリティ、そして「電磁鋼板」の今後の需要に対する先見の明が功を奏し、電磁鋼板の需要は拡大します。そして開業から5年で工場移転、増築、シャーリング加工の設備(電磁鋼板を板状に切る設備)を整え加工販売へ進出します。
幕張工場の始まり
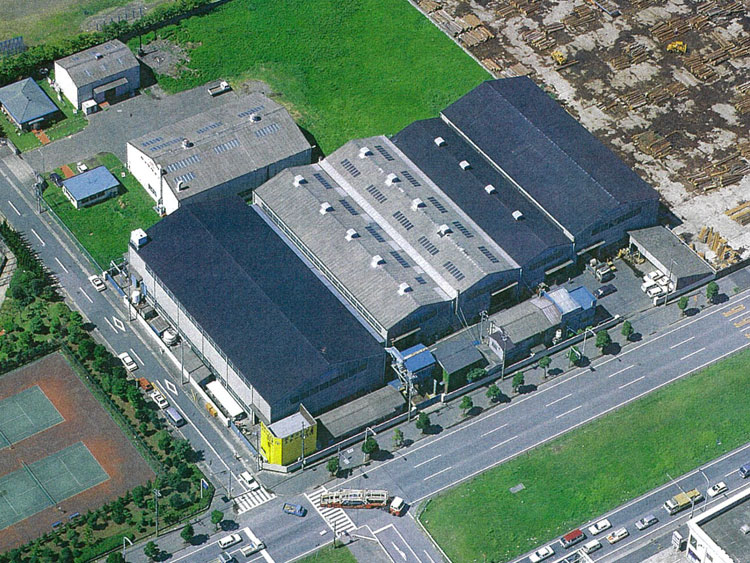
昭和30年、個人商店から会社組織へと移行すべく「有限会社松本商店」を設立、その2年後に「株式会社松本商店」がスタートします。やがて電磁鋼板の製造は熱間圧延の板材だけでなく、冷間圧延のコイル材(ロール状の電磁鋼板)へと移行期を迎え、松本商店は自社でコイル材をスリット加工(ロール状の電磁鋼板を切る加工のこと)すべく、新たに工場を立ち上げます。昭和40年以降は取引先がさらに増加し、その受注に対応すべく分散していた技術と設備、業務を集結するための用地を幕張に取得し、幕張工場が稼働を開始します。
熱間圧延と冷間圧延について
電磁鋼板の製造は、材料の磁気特性や用途に応じて、冷間圧延または熱間圧延のどちらかを選択することが一般的です。特に薄い帯状の電磁鋼板は、冷間圧延によって製造されることが多く、熱間圧延も特定の用途においては有用である場合があります。
熱間圧延は、金属を高温(通常は再結晶温度より高い温度)で加工する方法で、金属が柔らかくなるため、薄く延ばしたり、形状成型したりする際の加工が容易になり、鋼板は粘り強いものとなります。一方で、高温にするための膨大なエネルギーと熱膨張による寸法の不均一で寸法精度が落ちる場合があります。
冷間圧延は金属を室温(常温)で加工する方法で、熱間圧延に比べ、寸法精度が高く、薄く硬い鋼板の製造が可能です。一方で金属の再結晶温度以下で加工する為、加工性は熱間圧延より劣ります。
この様な特性から、熱間圧延電磁鋼は自動車のフレームやガードレール、建築資材などに、冷間圧延電磁鋼は家電、電子機器、PC向けの部品などの製造にと、用途に合わせて使い分けられています。なお、弊社が現在素材として仕入れているのは「冷間圧延電磁鋼板」です。
プレス加工のはじまり

電磁鋼板のスリット加工工場としてスタートした幕張工場に、新たな転機が訪れます。当時参加していた勉強会がきっかけとなり電磁鋼板プレス加工の話が持ち上がり、兼吉は新しい分野に進出する事を決意します。スリット販売から、プレス加工工場としての新たな挑戦が始まります。その後は大きな取引の開始と、お取引先からの設備や技術の移管により、事業は更に拡大します。
トップクラスの精密加工工場「白井工場」誕生へ
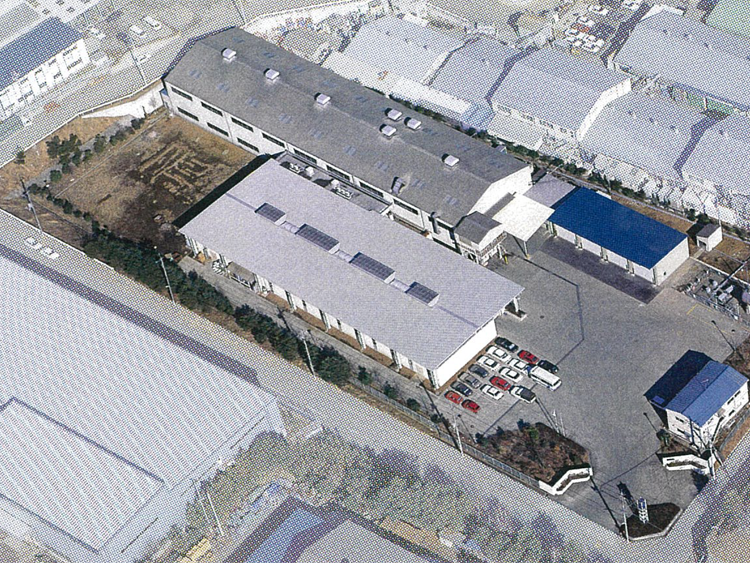
昭和45年、電磁鋼板(ケイ素鋼板)の加工会社と一目でわかるように「松本シリコンスチール工業株式会社」へと社名が変更されます。この社名は社内一般公募により選ばれ、命名者には賞金が出されました。
その10年後、手狭になった幕張工場から「精密加工」部門を集結すべく、「白井工場」を建設します。プレス機、焼鈍炉、ダイカスト設備を備え、のちに国内トップクラスの電磁鋼板精密加工センターと言われる白井工場の歴史が始まります。
東北への進出と「鶴岡工場」の誕生
素材の納品先があった山形県鶴岡市に東北地方への電磁鋼板販売とモーター・コア加工を目的として、昭和58年に鶴岡工場が誕生します。白井工場からの設備移設や新たなプレス機、ダイカストマシンなどの導入により、少数精鋭で製造から出荷までの業務を担う鶴岡工場が誕生します。
製品(モーター・コア)ができるまで
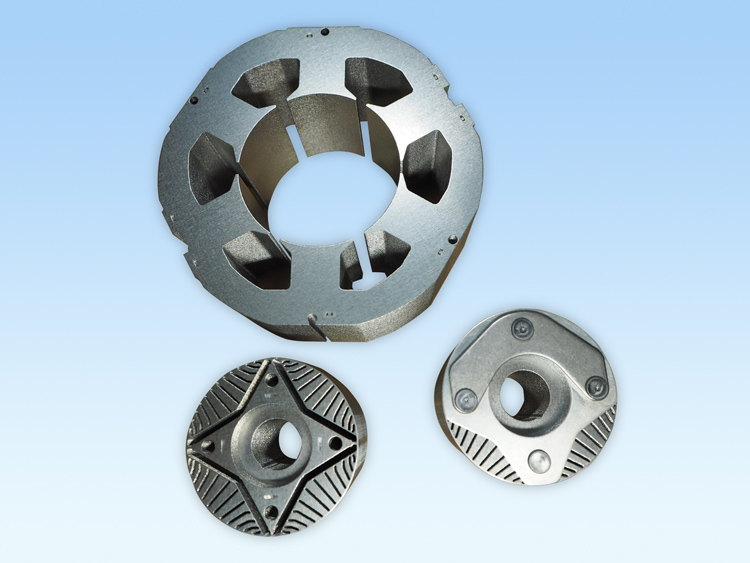
前章では松本ESテックの歴史から各工場の誕生を紹介しました。ここからは、各工場の特徴と、どのような工程を経て電磁鋼板を加工し製品が完成するのか、作業の流れはどういったものなのかを、技術面についてもふれながら紹介します。
幕張工場の工程
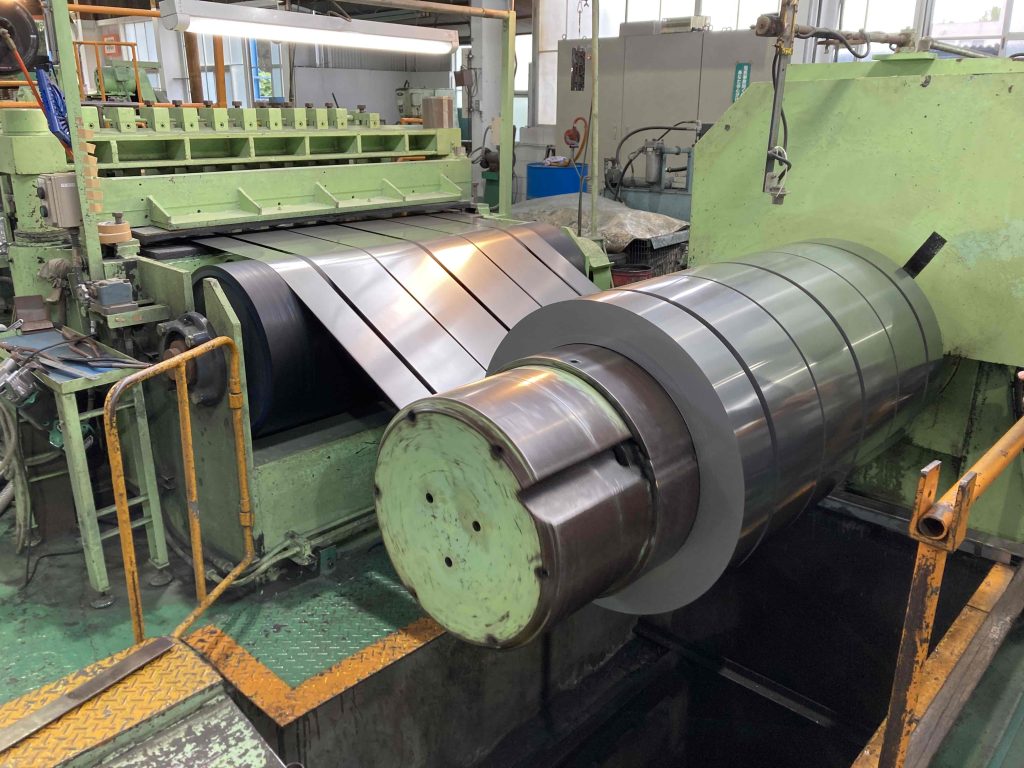
幕張工場は幕張駅から徒歩15分、立地条件はとても良く、定時間内で仕事をコントロールしやすい職場環境の為、自分の時間を大切にしたい、そんな社員が多く働いている工場です。本社も幕張にあるため、意思決定から実行までのスピードが他の工場と比べてとても速いのも特徴の一つです。
スリット加工
幕張工場では電磁鋼板を仕入れ、お客様の指示に従いカットし、梱包して出荷する作業と、白井工場プレス工程への素材提供の2つの作業を担っています。ロール状にクルクルと巻かれた電磁鋼板を伸ばして一定の幅、長さに切断し、再度ロール状に巻きあげる工程はスリット加工工程と呼ばれており、幕張工場は現在、スリット加工専用の工場となっています。
仕入れた電磁鋼板は床上操作式クレーンでトラックの荷台から下ろし、スリットの機械にセットしカットします。板の厚さが均等でなかったり、癖があったり、中には0.2㎜程の薄い材料もあったりするので、その特性に合わせた生産をすることがとても難しく、データの蓄積を細かく行いセッティングに細心の注意を払う事で対応しています。また、仕入れた電磁鋼板は(通常は母材と呼びます)大きいもので13t前後/個、スリット加工後の製品は30k/個~4t前後/個と大変重く、クレーン操作必須の作業です。(※クレーンの資格は入社後取得できます)一日でスリット加工する電磁鋼板処理量は多い日で100t前後/日と、日常の生活ではなかなか想像し難い超重量級の製品を扱う工場ですが、少量、短納期を実現する小回りを利かせた対応力が強みの工場です。
白井工場の工程
国内有数の最新型高速プレス機、周辺設備を導入した白井工場は当社のメイン工場で、2022年には白井第二工場第3棟も稼働開始しました。系列外、個人事業主での電磁鋼板の精密加工センターとしては国内最大級の規模、試作案件にも対応できる技術と設備を兼ね備えた工場です。白井工場には複数の工程があり、お客様の多様なニーズに応えるべく体制を整えています。
プレス工程
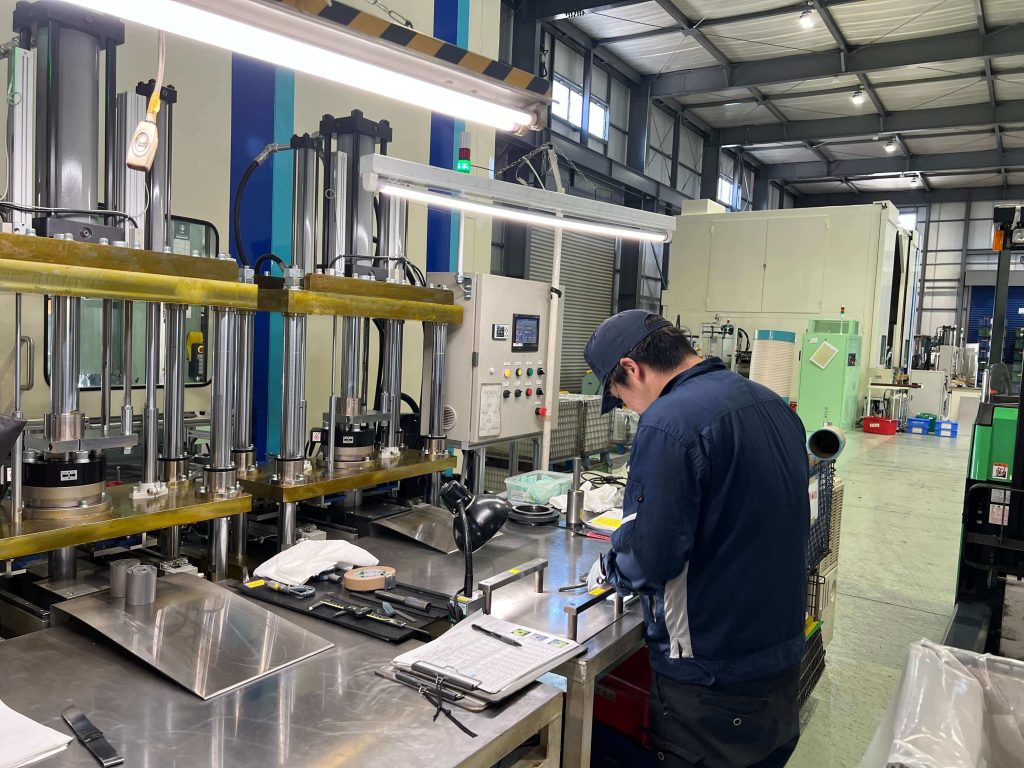
幕張工場でスリット加工された電磁鋼板をプレス加工機にセットし、打ち抜いて重ね、圧を掛け製品(モーター・コア)が完成します。お客様が必要とするモーター・コアの形状、特性はそれぞれ異なるため、ご注文ごとに打ち抜くための型(金型といいます)をセットする段取りも大切な仕事の一つです。この型替え作業を正確に行い、機械が稼働するまでベテランでも約8時間かかります。そしてスタートボタンが押された高速プレス機は毎分260~300ショットのスピードでモーター・コアを作り上げます。従業員は完成した製品をチェックし、次の工程に引き継ぎます。
ローター組立工程
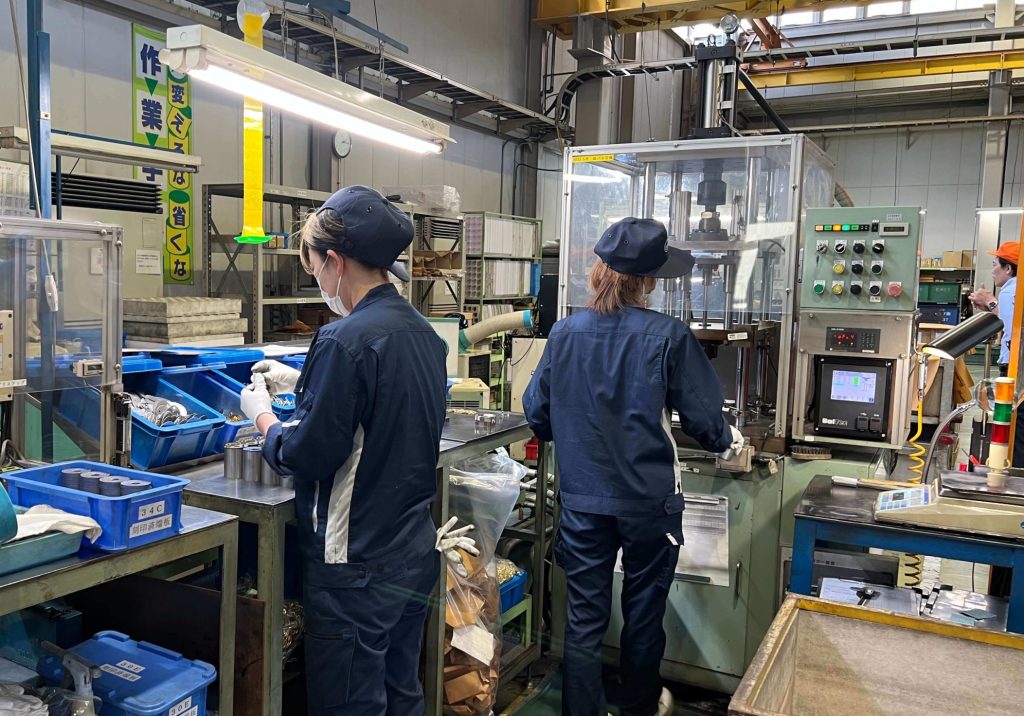
この工程では小型のモーター・コアにお客様のご要望に合わせて、マグネットや指定部材などの部品を取り付ける作業を行っています。エンド工程のため上工程からの影響を受けやすく、不適合品の流出防止のチェックと納期厳守意識の高い工程です。製品にもよりますが、新人が作業する生産量は30個/時、一年後50個/時と成長が数字で分かるため、ゲームの得点をクリアする様な感覚で目標設定がしやすい工程です。
焼鈍(しょうどん)工程

プレス工程から引き継いだモーター・コアを焼きなます工程です。炉の温度は780度にまで上がり、炉の温度を下げない管理が必要となるため、稼働期間中は24時間体制の工程です。焼鈍加工はプレス加工により外力が加わり、悪化した電磁鋼板の鉄損を回復させる為に必要な歪取りとして、お客様のご要望に応じて対応しています。モーター・コアが入った鉄箱を焼鈍炉に入れ、約9時間焼きなまし、取り出して冷まし製品が完成します。この作業もフォークリフトやクレーンを扱う資格が必要です。
製造技術工程
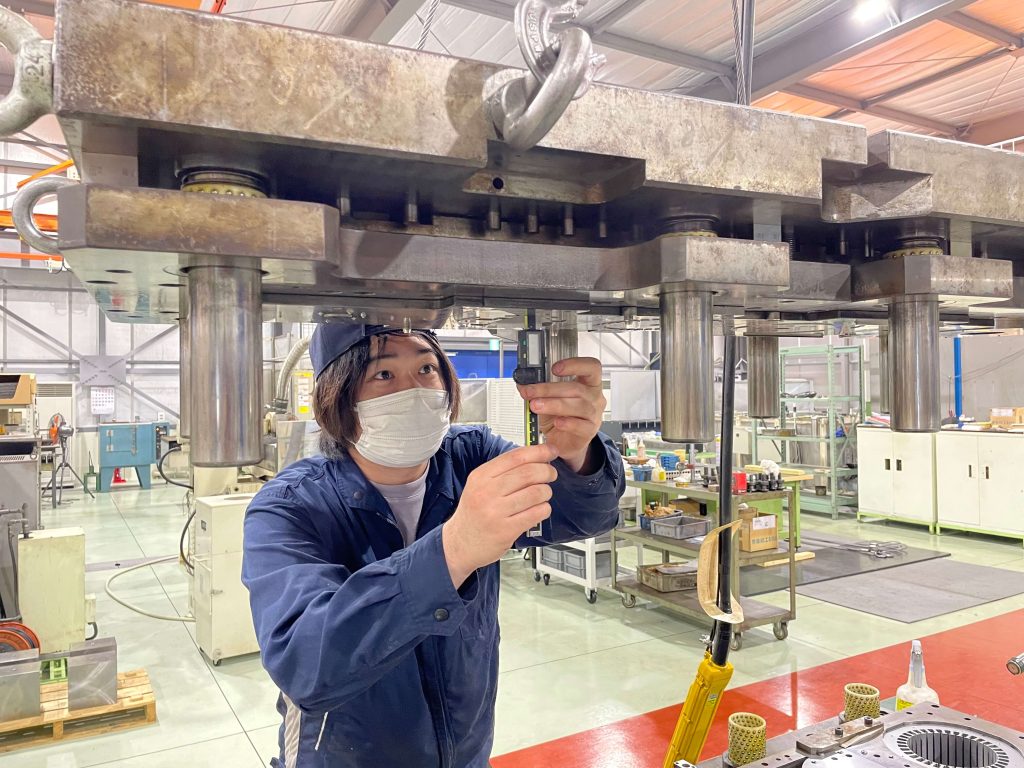
(金型メンテナンスグループ)
プレス加工機で使用する、製品を造り出す要である「量産順送金型」をメンテナンスし、維持、管理している工程です。メンテナンスでは金型を一つ一つ外し、研磨したり、丁寧に掃除をしたりしながら組み上げて元の金型の部品に戻していきます。金型の精度を維持し管理する技術と、プレス生産時のトラブルにもスピーディーに対応できる体制が弊社の強みでもあります。
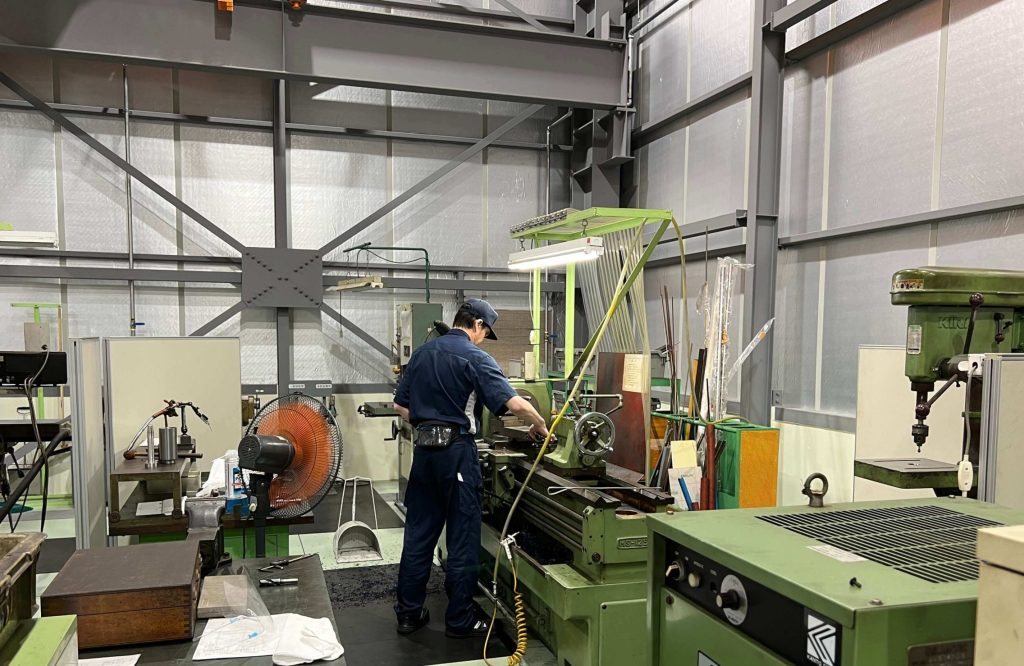
(試作グループ)
同じ製造技術工程でもこちらのグループは、量産を見据えた試作案件に対応しているグループです。ワンパンチプレスという、手動操作のプレス機で試作品を一つ一つ作り上げるだけでなく、試作金型や治具の設計、製作にも対応できる技術を持ち合わせています。
製造技術工程は弊社の精密加工「製造技術」が集結している工程です。
品質管理
品質管理部門は製造工程パトロール、受入検査、製品データどり、出荷検査など、正しい工程で生産しているか、正しい規格で生産されたか、出荷した製品に不具合はないか、を確認、管理する部門です。三次元測定機などを利用し製品を確認しています。
生産管理
全ての生産活動は生産計画により実施されています。お客様からの注文に対する仕入れから人の配置、生産の計画までを管理する「製造工程における司令塔の役割」を生産管理は担っています。
全工場にそれぞれ配置されている生産管理部員は常に社内外とコミュニケーションを取りながら業務を行っています。
鶴岡工場の工程
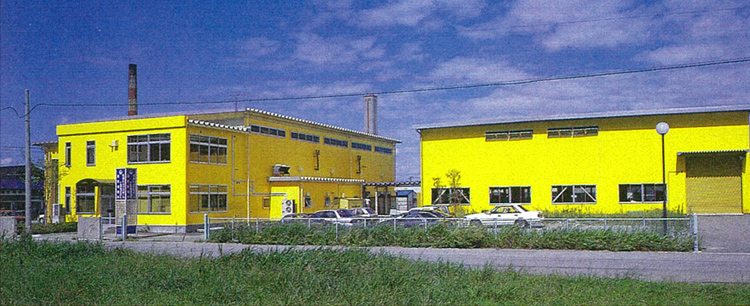
唯一千葉県外にある鶴岡工場は鶴岡の東工業団地あり、主にファンモーター用のローター(回転する側)とステーター(銅線を巻いた固定された部分)を出荷しています。
プレス工程
幕張工場でカットした材料をプレスの機械にセットし打ち抜いて重ね、圧を掛け製品(モーター・コア)が完成します。
ダイカスト工程

ローター(回転する側/回転子)に溶かしたアルミを付着させる事で電磁特製や形状を変化させることができます。ダイカスト工程では、ダイカストマシンの溶解炉で溶かした純度の高いアルミが自動的に金型に流れ、ローターに付着させていきます。その後冷却され、出来上がった製品の工程内検査を行います。
ルミラー挿入、クマドリ溶接工程
この工程は弊社では鶴岡工場のみが行っています。ルミラー挿入とは絶縁フィルムをステーター(固定された側/固定子)に挿入する作業、クマドリ溶接はローターの銅線を溶接する作業です。
松本ESテックの優位性とは
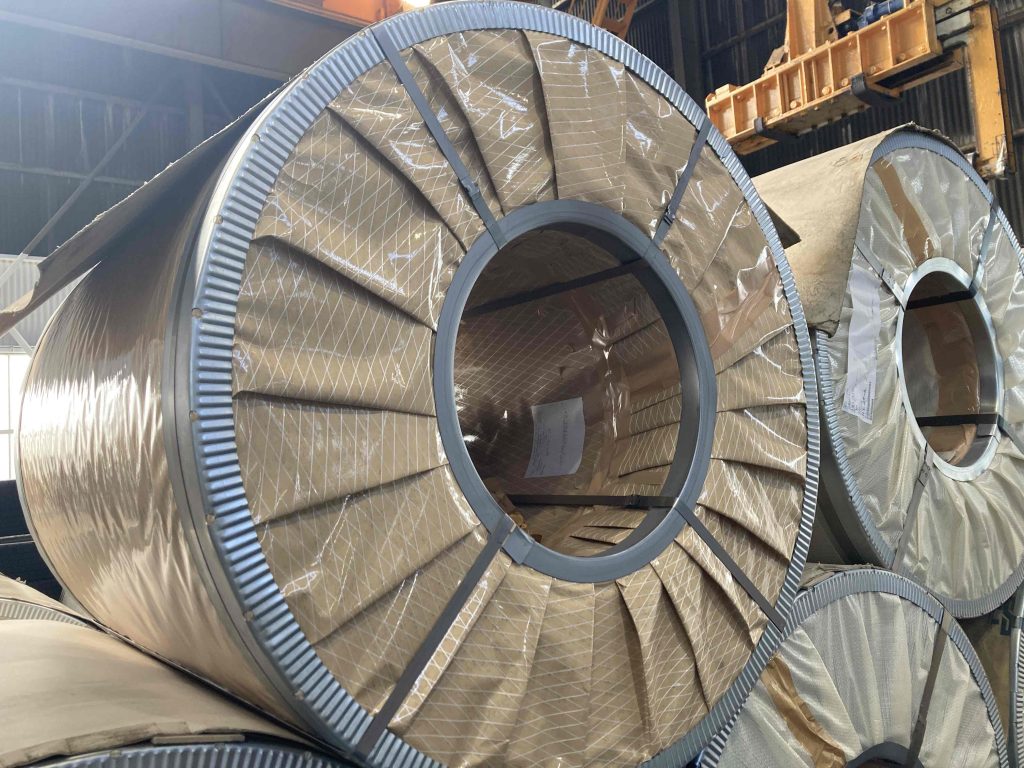
板の状態から帯の状態に変わり始めた頃の電磁鋼板は、巻きぐせが強く、当時スリット加工の技術開発には苦戦を強いられました。その当時のスリットマシンは50年以上働き、今もなお現役で活躍しています。時を経て積み上げてきた実績と数えきれない程のデータの数々、継承され続けているアナログ的な情報は、スリット工程には欠かす事の出来ないものとなっています。
対照的に、弊社のプレス機は年季の入った物から超最新型高速プレス機まで、お客様からの多種多様なニーズに対応すべく、設備を整えています。オペレーション教育も機種ごとに行われ、プレス機の要ともいわれている金型を維持管理する技術は当社の宝です。諸先輩方の歴史と最新技術の融合がプレス工程を支えています。
更に優位性を高めるべく、複数会社の電磁鋼板を仕入れる事で、さまざまなお客様のご要望にお応えする事が可能になりました。弊社の技術は創業当時から蓄積され、継承された実績と、変わりゆく時代に乗り遅れる事のない様投資を続ける設備、そして最高の製品をお客様に届けたい、という社員の思いによって守られています。
一緒に働いてみませんか?
新卒採用はもちろん、中途採用も不定期で行っています。技術を必要とする仕事ですが、経験の必要はありません。現在弊社で活躍している社員も知識ゼロからスタートした社員ばかりです。必要なのは「やる気」と分からない事を分からないと言える「素直な気持ち」です。分かるまで丁寧に教えますのでご安心下さい。募集状況などの詳細は採用情報をご確認ください。
まとめ
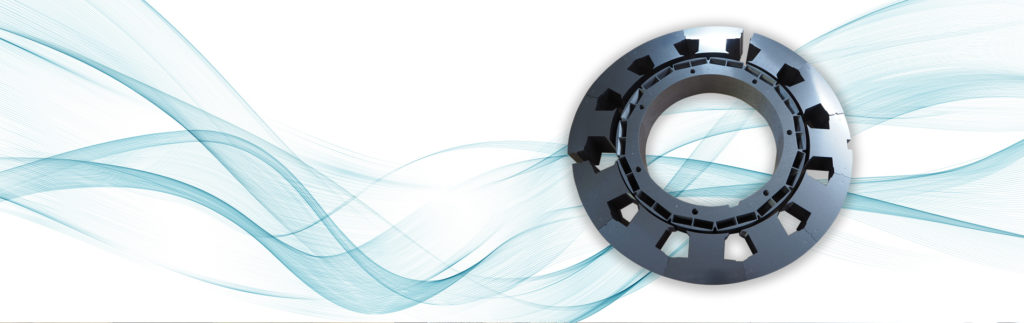
今回は松本ESテックの歴史から各工場の始まりと特徴、工程ごとの作業内容、弊社の技術と優位性についてお伝えしました。同じ会社内でもそれぞれの工場ごとに(工程ごとにも違います)社員の様子も仕事内容も異なります。身近な仕事ではないため文字で説明するより、目で見て確かめて頂くのが1番!いずれは動画などでご紹介できればと考えています。